1.1- BIOETHANOL
1.1.1- COMPOSITION
Ethanol (C2H5OH), commonly known as ethyl alcohol, is an organic, colourless, volatile, greatly flammable alcohol which is water soluble, hygroscopic (tends to absorb water from the air) and non-toxic for humans, although it is a psychoactive drug if consumed. As a biologic substance, it is biodegradable, so it does not result specially contaminating in case of spilt. Due to the possibility of synthesising this alcohol from fossil hydrocarbons, the organic kind is also called bioethanol in order to avoid misunderstandings.
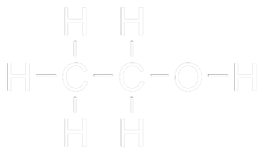
Its combustion forms water and carbon dioxide, producing heat.

1.1.2- HISTORY AND RELEVANCE
A technologically simple obtaining, along with abundant prime matter accessibility, mad e ethanol become the first great scale liquid combustible used during the final 19th century in the USA in scopes such as public illumination and, later, automotion.
The historic relationship between the car and this combustible is more than significant: the first Nicholas Otto's internal combustion engine, the precursor of the modern Otto-cycle engine, ran, in the 1876, with mere corn ethanol. Forty years later, Henry Ford recognised it as "the fuel of the future", and designed his earliest vehicle, the Quadricycle, to run purely with this vegetal-originated hydrocarbon. His posterior Ford T could perfectly fit in both ethanol and gasoline.
Nowadays, after more than half a century of a low-consumption period, during which gasoline and gas-oil have fed virtually alone this energetic market around the globe, the use of bioethanol is gaining relevance in countries like Brazil, where private cars have progressively turned into this combustible made from national sugarcane since the 70's oil shock, and its national oil importing has dropped a 40% up from then; Sweden, whose government requires, by law, all service stations to sell bioethanol; or the USA, where the government has been subsiding corn ethanol since 1978 and its current production capacity is of 46,94 gigalitres.
|
|
Henry Ford's ethanol-fed Quadricycle.
Source: <http://www.lessignets.com/signetsdiane/calendrier/images/
juillet/30/ford_quadricycle16.jpg>
|
Brazilian sugarcane harvesting. This is the most efficient 1G nationwide ethanol production system currently existing.
Source: <http://knowledge.allianz.com/nopi_downloads/
images/sugarcane_zoom.jpg> |
1.1.3- PROPRIETIES AND CHARACTERISTICS IN ENGINE. APPLICATIONS
Commonly, ethanol is used as a substitute for gasoline, pure or blended, in automobile internal combustion Otto cycle engines.
The most positive ethanol technical characteristic in its use as a combustible is its higher octane grade (around 116 AKI in a 95% of pureness compared with the 90-98 AKI of gasoline), what is traduced into a higher efficiency and torque power, requiring a higher piston compression ratio. However, there is an important disadvantage: ethanol is a highly corrosive substance that results aggressive to metals such as aluminium, magnesium or zinc and copper alloys and elastomers like the ones used in the pipes; that makes standard ICV engines incapable to work on this alcohol without suffering a higher wearing.
In conclusion, those should be the changes made in an ethanol-tolerant engine:
Increase of the spark plug power due to the higher minimal oxidation temperature.
Increase of the mechanical resistance of the cylinder, valves, valve seats and piston due to the higher compression ratio.
Nickel-coated carburettor and chromed combustible bombs in order to avoid engine corrosion.
Use of other materials in pieces which could be corrupted (elimination of all aluminium, magnesium and rubber parts).
Combustible pipes made in nylon.
Lead or pewter treatment in the fuel tank.
There are no commercialized pure-ethanol vehicles due to the inexistence of a reliable alcohol supply; consequently, carmakers have designed a car which can run both on gasoline and ethanol (in any mixture), called flexible fuel vehicle (FFV), optimising the pressure ratio and the ignition time depending on the fuel in the tank.
Then, ethanol can be used in conventional cars in blends of 15% or less, that is, E5, E10 and E15, without neither producing any trouble in non-adapted motors nor requiring any modification in them.
1.1.4- OBTAINING
T HROUGH FIRST GENERATION METHODS:
The actual current industrial obtaining of bioethanol consists, basically, in producing and grinding great quantities of vegetable crops with high sugar content, fermenting them later with the aid of appropriate microorganisms and finally distilling the product to make it able to be used.
The vegetable matters able to produce ethanol are starches (i.e. corn, potato and cereals in general) and sugars (i.e. sugar cane, beetroot, molasses, etc.). Once obtained them via grinding the crops, it is necessary, in the case of the starches, to decompose those particles into maltose through hydrolysis using the a-amylase enzyme, and cracking them again with the aid of glucoamylase into pure glucose by the saccharification process.
· Hydrolysis

· Saccharification
In the case of sugar-rich crops, it is convenient to omit the hydrolysis and directly perform the saccharification with another enzyme, invertase, because it will not be maltose but with sucrose, a disaccharide of fructose and glucose.
· Saccharification

Once having the monosaccharide sugars (as glucose or fructose), the following process is the fermentation of that substance with the Saccharomyces cerevisiae yeast. In this reaction, glucose and fructose are digested and converted into ethanol and CO2 as metabolic waste. This operation requires a pressure of between 4800-7200 kPa, and a temperature of 29-35 ºC.
The product obtained by the fermentation is a low alcohol-graded liquid mixed with water which must be first distilled until up to 96% of pureness is achieved, what could be adequate to be used as a fuel alone. However, if the intention is to blend it with gasoline, a purity of more than 99% must be attained. Since the result is an azeotropic mixture (water can't be separated by simple distillation), the alcohol must be dehydrated through certain complex processes.
Finally, the last step is denaturing this alcohol to make it unfit for human use, given that ethanol for beverages is highly taxed and regulated by governments, a handicap that the energetic kind does not suffer. This denaturalisation is performed with the addition of toxic hydrocarbons such as methanol or benzoate, in general.
|
Schematic diagram of production process of bioethanol from corn grains
Graphic source: <http://www.cropenergies.com/en/Bioethanol/Produktionsverfahren/Schema-e_1_1.pdf> |
THROUGH SECOND GENERATION METHODS:
Second generation biofuels (aka 2G) are those extracted from residual or non edible vegetal matter (i.e. cellulose in general, non-alimentary crops and organic farm waste) through alternative chemical processes that make possible to obtain fuels such as ethanol or biodiesel from that kind of feedstock. Those methods are still under development and implantation, and they play a small role in the biofuel markets.
In the particular case of bioethanol, the main difference between 2G and 1G processes is that the sugars are obtained not from edible parts of a plant, but from the cellulosic matter (most of the organic biomass), which is formed by long chains of glucose that must be broken down into hemicelluloses before hydrolysing and fermenting it. The steps to follow to obtain ethanol are these: primary treatment, hydrolysis, microbial fermentation, distillation and dehydration.
The primary treatment or pre-treatment consists on separating the glucose chains of the lignin crystalline structure that contains them. The most currently used method is the steam explosion process (SEP or autohydrolysis), that consists on exposing the fibre to high pressurized steam (between 1300 and 3102 kPa, with a temperature around 100ºC) and depressurise it explosively to the same level as the atmosphere repeatedly, disintegrating the biomass into separate fibers . This system has been largely applied in new cellulosic ethanol plants, such as the Abengoa's one placed in Babilafuente (Salamanca), which transforms cereal straw into this alcohol in order of 5-milion-liter per year, being a world pioneer in this area.
Once realised the primary treatment, the subsequent steps are the ones described in the previous section.
|
Abengoa's 2G ethanol factory in Babilafuente
Source: <http://www.greencarcongress.com/images/babilafuente.jpg>
|
THROUGH THIRD GENERATION METHODS:
Any biofuel obtaining process what involves the cultivation of bacteria or algae is considered a third generation method (aka 3G). Those systems, as well as second generation methods, are decades far from being applied in a medium or great scale, since they are still under development.
Traditionally, the lipid-rich macro algae have been mainly contemplated as a source of oil to elaborate biodiesel (see the chapter 1.3.4.3). However, once this lipid portion has been extracted, there's a residual starch and cellulosic fraction that can be fermented into ethanol, so this 3G method can make possible to generate both kind of biocombustibles from an only crop.
|